5 Steps to Minimizing Combustible Dust Explosion Risks
Time to Read: 3m 23s
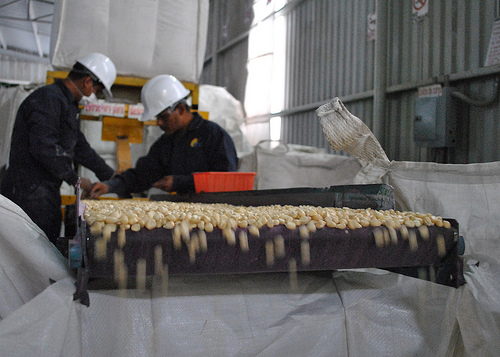
Combustible dust can be a major safety hazard in industrial settings. Nearly any dry bulk material will create a certain amount of combustible dust, and some materials, particularly those with particle sizes less than 40 mesh—sugar dust, coal dust, sawdust, corn dust, and others—are especially prone to combustion. This dust is one of five elements needed to produce a combustible dust explosion:
- Fuel to burn (combustible dust)
- Ignition source (sparks, heat, etc.)
- Ambient oxygen
- Dust cloud concentration (focuses combustible energy into an explosion)
- Dispersion of dust particles
1. Avoid Providing Fuel for An Explosion
If your facility processes dry materials, you’re producing fuel for a potential combustible dust explosion. Even certain materials that are not considered flammable or combustible in their “normal” state can become combustible as dust. The create and accumulation of this dust are all but inevitable. Ergo, minimizing the fuel source is key. Nol-Tec Systems’ Air Assist technology uses high-pressure, low-volume air flow to convey materials. An Air Assist pneumatic conveying system provides a gentler, less abrasive conveyance process, which reduces product breakage and, therefore, dust production. Air Assist also prevents your material—and its dust—from dropping out of the conveyor flow and accumulating. The motive air keeps dust moving to an appropriate collection point.2. Avoid Ignition Sources in Your Process
Material processing equipment provides numerous potential ignition sources—overheating bearings and belts, sparks caused by out-of-alignment components, system blockages, and even slightly above-average operating temperatures. Monitoring the entire system for possible ignition sources can be difficult (nigh impossible), so removing as many of these sources as possible is important. Pneumatic conveyor systems—like Nol-Tec’s Air Assist systems—require far fewer moving parts than fully-mechanical systems. Fewer moving parts produce less friction, which, in turn, significantly sparking and heat sources. Nol-Tec can also develop special automated controls and monitoring devices to enhance process safety. These precision controls can be integrated throughout your facility, enabling you to monitor your processing equipment and address equipment problems before they become potential ignition sources.3. Minimize Ambient Oxygen
As oxygen is all around us, everywhere, at all times, it is impossible to completely remove it from the ambient atmosphere of your processing environment. However, the concentration of oxygen and combustible dust can be controlled and kept at safe levels that will prevent combustion. Replacing the oxygen in a pneumatic conveying system with an inert gas, such as nitrogen, can remove the potential combustible dust explosions. Gas inerting, as this process is called, can also eliminate the need for costly explosion mitigation and suppression modifications to your processing system. Nol-Tec Systems has partnered with Air Products & Chemicals to research a system that would prevent dust explosions via gas inerting. A co-authored paper with the companies’ findings can be found in the March 2015 issue of Chemical Engineering.4. Avoid High Dust Particle Concentration
Before it truly becomes an explosion hazard, combustible dust must be in a high enough concentration in the atmosphere. The NFPA (National Fire Prevention Association) has developed formulas for calculating the hazardous concentration levels of numerous materials. To minimize the potential for combustible dust explosion in your facility, both your materials and your system/equipment need to be evaluated individually. Nol-Tec’s design team can work with you to design a pneumatic conveyor system that provides the performance you need and improves processing safety.5. Properly Disperse Combustible Dust
Though it is crucial to avoid the accumulation of combustible dust particles (see #4), some methods of dust dispersion are better than others. With the proper dust containment and collection devices in place, material dust can be safely controlled and disposed of. Nol-Tec’s Air Assist pneumatic conveyors make it easy to contain, collect, and remove process dust from the system, thereby minimizing the risk of combustion. Nol-Tec offers the most effective solutions for minimizing dust explosions.For more information, visit www.nol-tec.com.